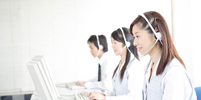
泊头市申泰量具厂
销售总机:0317-5560000
公司电话:0317-5560000
7*24服务热线:13833711135
公司传真:0317-7870444
公司邮箱:bt0317@163.com
公司地址:河北省泊头市工业开发区
华东地区:13131772330
华南地区:13131772331
华西地区:13131772339
华北地区:15720440949
- 机床铸件的生产工艺 [2014-03-22]
1、机床床身铸件生产工艺:我公司有一条完善的树脂砂生产线,各种机床床身铸件均采用树脂砂、消失模铸造。这种工艺使得铸件尺寸精度高,均匀一致,不扣箱,铸件无飞边、毛刺;表面光滑度接近精密铸造,内部结构稳定,排除或降低了砂眼、气空等铸造缺陷,整个生产过程三级环保,没有污染。
2、机床床身铸件的材质:为优质的高强度铸铁HT250-300,抗拉力强,使用寿命长。3、机床床身铸件的退火处理:铸件经过两次人工时效处理,去除内应力。铸件内部结构稳定,不易变形。4、超大规格的机床床身铸件可拼接制作,铸件时可分开来铸。加工时进行整体加工,使其保证安装及使用精度。
- 床身的铸造方法和选择原则 [2014-03-22]
数控机床床身铁铸件的铸造方法常用的是砂型铸造,其次是特种铸造方法,如:金属型铸造、熔模铸造、石膏型铸造等。而砂型铸造又可以分为粘土砂型、有机粘结剂砂型、树脂自硬砂型、消失模等等。
机床床身铸造方法选择的原则:1优先采用砂型铸造,主要原因是砂型铸造较之其它铸造方法成本低、生产工艺简单、生产周期短。当湿型不能满足要求时再考虑使用粘土砂表干砂型、干砂型或其它砂型。粘土湿型砂铸造的铸件重量可从几公斤直到几十公斤,而粘土干型生产的机床床身铸件可重达几十吨。2根据铸造方法使其与批量生产相适应。低压铸造、压铸、离心铸造等铸造方法,因设备和模具的价格昂贵,机床床身适合批量生产。机床床身铸件等大型模具较之传统砂型有很大优势,它不但省去了昂贵的木型费用,而且便于操作,缩短了生产周期,提高了生产效率,具有尺寸精度高,加工余量小,表面质量好等优势。
- 铸造机床床身铸件材质的选用 [2014-03-22]
铸造机床床身铸件材质的正确选用:
机床床身材料大多选用灰铁铸铁材质,也有极少量的铸钢机床床身,现代机床床身设计中用结构钢焊接的床身比例逐渐上升。机床床身铸件有良好的尺寸稳定性,用来做机床床身不宜变形,有利于长期保持机床精度。1、铸铁机床床身有良好的铸造性能,便于铸造出各种复杂结构的形体;2、与钢相比铸铁虽然抗拉强度较低,但抗压强度与钢接近,大多数机床床身对抗拉强度要求不高,完全可以满足性能要求;3、铸铁材质有良好的减震性能,更有利于避免机床运转时产生震动,降低噪音。4、灰铁材质铸造床身有良好的润滑性能,结构中的微孔可以容纳较多润滑油,同时含有的碳元素有自润滑作用。5、相对于一般钢材来讲,铸铁床身铸件有良好的耐锈蚀性能,便于保持机床导轨的精度。
- 铸件影响质量的因素 [2014-03-22]
影响铸件质量的因素很多,第一是铸件的设计工艺性。进行设计时,除了要根据工作条件和金属材料性能来确定铸件几何形状、尺寸大小外,还必须从铸造合金和铸造工艺特性的角度来考虑设计的合理性,即明显的尺寸效应和凝固、收缩、应力等问题,以避免或减少铸件的成分偏析、变形、开裂等缺陷的产生。第二要有合理的铸造工艺。即根据铸件结构、重量和尺寸大小,铸造合金特性和生产条件,选择合适的分型面和造型、造芯方法,合理设置铸造筋、冷铁、冒口和浇注系统等。以保证获得优质铸件。第三是铸造用原材料的质量。金属炉料、耐火材料、燃料、熔剂、变质剂以及铸造砂、型砂粘结剂、涂料等材料的质量不合标准,会使铸件产生气孔、针孔、夹渣、粘砂等缺陷,影响铸件外观质量和内部质量,严重时会使铸件报废。第四是工艺操作,要制定合理的工艺操作规程,提高工人的技术水平,使工艺规程得到正确实施。
铸造生产中,要对铸件的质量进行控制与检验。首先要制定从原材料、辅助材料到每种具体产品的控制和检验的工艺守则与技术条件。对每道工序都严格按工艺守则和技术条件进行控制和检验。最后对成品铸件作质量检验。要配备合理的检测方法和合适的检测人员。一般对铸件的外观质量,可用比较样块来判断铸件表面粗糙度;表面的细微裂纹可用着色法、磁粉法检查。对铸件的内部质量,可用音频、超声、涡流、X射线和γ射线等方法来检查和判断。
- 机床床身分析退火种类 [2014-03-22]
常见的退火工艺有:再结晶退火,去应力退火,球化退火,完全退火等。退火的目的:主要是降低金属材料的硬度,提高塑性,以利切削加工或压力加工,减少残余应力,提高组织和成分的均匀化,或为后道热处理作好组织准备等。1.完全退火和等温退火完全退火又称重结晶退火,一般简称为退火,这种退火主要用于亚共析成分的各种碳钢和合金钢的铸,锻件及热轧型材,有时也用于焊接结构。一般常作为一些不重工件的最终热处理,或作为某些工件的预先热处理。2.球化退火球化退火主要用于过共析的碳钢及合金工具钢(如制造刃具,量具,模具所用的钢种)。其主要目的在于降低硬度,改善切削加工性,并为以后淬火作好准备。3.去应力退火去应力退火又称低温退火(或高温回火),这种退火主要用来消除铸件,锻件,焊接件,热轧件,冷拉件等的残余应力。如果这些应力不予消除,将会引起钢件在一定时间以后,或在随后的切削加工过程中产生变形或裂纹。
- 机床铸件的凝固方式 [2014-03-22]
机床铸件的凝固方式1、逐层凝固方式,合金在凝固过程中其断面上固相和液相由一条界线清楚地分开,这种凝固方式称为逐层凝固。常见合金如灰铸铁、低碳钢、工业纯铜、工业纯铝、共晶铝硅合金及某些黄铜都属于逐层凝固的合金。2、糊状凝固方式合金在凝固过程中先呈糊状而后凝固,这种凝固方式称为糊状凝固。球墨铸铁、高碳钢、锡青铜和某些黄铜等都是糊状凝固的合金。3、中间凝固方式 大多数合金的凝固介于逐层凝固和糊状凝固之间,称为中间凝固方式。中碳钢、高锰钢、白口铸铁等具有中间凝固方式。机床铸件凝固方式的影响因素 1、合金凝固温度范围的影响 合金的液相线和固相交叉在一起,或间距很小,则金属趋于逐层凝固;如两条相线之间的距离很大,则趋于糊状凝固;如两条相线间距离较小,则趋于中间凝固方式。 2、机床铸件温度梯度的影响 增大温度梯度,可以使合金的凝固方式向逐层凝固转化;反之,机床铸件的凝固方式向糊状凝固转化。
- 铜铝铸造之铸造关乎哪些方面? [2014-01-10]
- 在铸造中,有一些因素是很重要的,我们要控制好,这样才能有好的铸造效果,对于铜铝铸造来讲,也是如此,所以下面小编就来讲解一下关于铸造的几个方面。方面一:铸造速度铸造速度,它是与铸锭液穴深度成正比的。如果铸造速度增大,那么会使铸锭液穴深度与温度梯度增大,从而会在液穴底部出现液穴区段,产生较大的收缩应力,最终会增大出现铸锭热裂纹的几率,所以我们应控制好速度。方面二:铸造温度良好的铸造温度,会使液体金属保持良好的流动性,从而减少组织应力,防止产生裂纹。一般铸造温度应根据材料种类和铸锭规格来进行确定。如果温度不合适,那么会增加内应力,使得铸件产生裂纹或者开裂。温度过低,也是不好的,因为这样会使铸锭表面产生冷隔、夹渣等缺陷,甚至裂纹,最严重的,则会使铸造无法继续进行下去。方面三:液面高度液面的位置也很重要,如果过低,那么会使材料的热裂纹倾向增大,严重的话会影响铸造的进程。液面位置过高,则会加大铸锭的偏析程度,所以,要保证有合适的液面高度,过高过低都不行。
- 铸造中,铸造材料种类和标准有哪些? [2014-01-10]
铸造的定义是什么?
答:铸造的定义是:它是一种能将金属熔化,然后将金属铸模成型的技术。
铸造的种类很多,铜铝铸造应用也是十分广泛,那,它所使用的原材料有哪些?有哪些这方面的技术标准吗?下面小编就来带领大家探讨这些问题。
一、金属炉料
1.生铁
(1)适用的标准是GB/T 718-2005,如果是块状生铁,则单个重量应在2到7千克之间。如果重量在这之外的,那么每批中不能超过总重量的10%。
(2)铁块表面要保持干净整洁,没有炉渣或者砂粒现象。
2.废钢
(1)适用的标准是GB 4223-2004,废钢中碳的含量应小于2%,硫和磷的含量不能大于0.05%。
(2)废钢的最大尺寸不能超过300mm,厚度应在2.5—30mm,单块重量为0.25—10kg。
(3)废钢中,不能混杂废铁、合金以及有害物等。
(4)废钢中不能含有杂质,更不能有易燃易爆品或者橡胶、塑料制品等,非金属夹杂物和管状物、封闭器皿等也不能有。
二、炉料合金
1.硅铁
(1)适用的标准是GB/T 2272-2009,其厚度不能大于100mm。
(2)块度为30到70mm,应按同一牌号组批,但含硅量的波动不能超过3%。
2.锰铁
适用的标准是GB/T 3795-2006,块度为30到70mm。
3.铬铁
适用的标准是GB/T 5683-2008,其内部和表面不能有非金属夹杂物。
4.铜
适用的标准是GB 466-82,铜的含量不能小于99.7%,其单块重量不能超过0.5千克。
- 高锰钢薄板类焊接平台铸件采用何种铸造方法 [2013-03-21]
因高锰钢耐磨性好些所以一般的焊接平台铸件采用高锰钢铸造成型。
目前我们采用普通砂型铸造,表面质量太差,经常出现冷隔,达不到要求。
高锰钢衬板因为他的表面要求精度不高,所以用一般的砂型铸造就可以了,如果钢水熔炼没有问题,那就是要采用合适的型砂,当然上面那位说的也不错,用树脂砂和水玻璃砂能好多了, 也可以采用树脂砂和水玻璃砂造型,把浇口设计到90尺寸处、设计内浇道、多设内浇口、把铸型稍微的放置一些坡度、让浇口的那一边稍微的高一些。
- 焊接平台铸件缺陷电弧焊处理方式及优缺点 [2013-03-14]
焊接平台铸件缺陷电弧焊处理方式是用铸铁焊条Z248进行焊补,焊补工艺分两种:
第一种:焊前预热至550℃-650℃,焊补后保温5-8小时;
第二种:工件焊前不预热,焊后保温3-4小时。
两种方法均易出现裂纹、硬点,焊补后不容易进行机械加工。焊条价格便宜。用镍基铸铁焊条Z308焊条焊补,焊层与焊层之间应停顿冷却至60℃以下,焊补区少气孔、裂纹产生,机械加工性良好,结合强度高、无脱落现象,因为机床导轨加工后吸油及焊条吹力的影响,易产生咬边、形成“焊补痕迹”,焊补区颜色与母材有很大区别,并且焊条价格昂贵。
传统的喷焊、电弧焊工艺,焊补后易产生裂纹,工件易受热变形,容易出现二次气孔,焊补处金属颜色与母材差异大是其共同的特点,这也是传统焊补工艺不能彻底解决机床导轨缺陷修复的根本原因。
- 生产HT250铸铁焊接平台铸件热节缩孔的解决方法 [2013-03-10]
HT250铸铁焊接平台铸件浇口处出现缩孔形成的原因主要是:浇口处的金属液的温度高与铸件的其它位置的温度(冒口处除外)在浇铸后的冷却速度比其它位置的底、此处的金属液成为其它位置的收缩补充品、而且直浇道和内浇口的金属液已成固体或以经无法补缩造成的。
控制方法是:
1,加大直浇道的直径和内浇口的截面积,千万不要降低直浇道的直径和内浇口的截面积、降低后会出现更多的缩孔。降低浇铸温度也能控制此处的缩孔,但是会引起其它部位更多的缩孔;
2,浇口过于集中必要时加分散浇口 ;
3,真空消失模可以解决此问题。
- 铸铁铆焊平台为什么要留加工余量 [2012-11-12]
为了加工出合格的铸铁铆焊平台,必须从毛坯上切去的那层金属的厚度,称为加工余量。加工余量又可分为工序余量和总余量。某工序中需要切除的那层金属厚度,称为该工序的加工余量。从毛坯到成品总共需要切除的余量,称为总余量,等于相应表面各工序余量之和。
在铆焊平台上留加工余量的目的是为了切除上一道工序所留下来的加工误差和表面缺陷,如铸件表面冷硬层、气孔、夹砂层,锻件表面的氧化皮、脱碳层、表面裂纹,切削加工后的内应力层和表面粗糙度等。从而提高工件的精度和表面粗糙度。加工余量的大小对加工质量和生产效率均有较大影响。加工余量过大,不仅增加了机械加工的劳动量,降低了生产率,而且增加了材料、工具和电力消耗,提高了加工成本。若加工余量过小,则既不能消除上道工序的各种缺陷和误差,又不能补偿本工序加工时的装夹误差,造成废品。其选取原则是在保证质量的前提下,使余量尽可能小。一般说来,越是精加工,工序余量越小。
- 铆焊平台机械加工的几个重要环节 [2012-10-11]
铆焊平台属于大型的铸铁平台,在机械加工的时候要在两个方面进行控制:
1、机床调整
1)、根据铸铁平台的被加工表面与刀具的相对位置,将横梁的高度调到适当的位置。
2)、将两个侧刀架的高度调到适宜刨削平板两侧面的位置。
3)、因铸铁平板的重量大,行程长,所以切削速度不宜选择过高。要在运行中调整行程长短,并要求在工作行程开始时能使刀具低速切入平板,在工作行程结束时能使刀具低速切出铆焊平台。
2、刀具的选择
1)、平头精刨刀。这种刀具的切削刃较宽且平直,适宜铆焊平台的精刨和半精刨用。
2)、机械夹固式尖头刨刀。适用于铆焊平台的粗加工或半精加工。
- 焊接平台铸造时确定浇注系统类型 [2012-10-04]
焊接平台铸造时确定浇注系统类型:
(1)顶注式浇注系统适用于重量小、高度小和形状简单的薄壁铸件,也适用于顶部补缩的中、小型厚壁铸件。
(2)底注式浇注系统适用于大、中型高度不大的厚壁铸件。也常用于容易氧化的有色金属材料,因为金属液能平稳地上升而无飞溅现象。
(3)中注式浇注系统广泛用于各种壁厚、高度不大而水平尺寸较大的铸件。
(4)阶梯式浇注系统应用于高大、复杂的大型的铸件。
- 铸铁平台平面度的误差如何评定 [2012-08-20]
铸铁检验平台平面度误差是指被测实践外表对幻想平面的变化量。在确定变化量巨细时,幻想平面相关于实践外表的详细方位起着决议性效果,由于分歧方位的幻想平面与实践外表上各点的间隔是分歧的。用于确定幻想平面方位的准则如下:
1、三点法准则规则幻想平面经过实践外表上相距最远且不在一条直线上的三点构成的平面为评定基面,以各测点距此平面偏向中最大值与最小值之差为所求被测外表的平面度误差值。
2、贴切准则用一个幻想平面与实践外表相切,且与实践外表之间的最大间隔为最小,此间隔为平面度值
3、最小二乘方准则将一个幻想平面按实践外表的趋势,置于实践外表的中部,并使实践外表上各点到幻想平面的间隔平方和为最小,以这个最小二乘方中间平面作为评定基面,各测点对此平面偏向中最大值与最小值之差为被测外表平面度误差值。
4、对角线准则以经过被测外表的一条对角线而平行于另一条对角线的平面作为评定基面,各测点对此平面偏向中最大值与最小值之差为被测面平面度误差值。
5、环线法准则应用测量闭合环的平差道理,使各被测点平差后的新地位到测量基面的间隔变为各点相关于幻想平面的间隔。这时幻想平面就是经过原点的天然程度面。
6、最小前提准则用两个平行的幻想平面容纳实践外表,并使两幻想平面间的间隔为最小,此最小间隔为平面度误差值。
以上几种评定的办法为最常用的方法,根据实际情况的不同我们应该采用不同的方法。
- 采用电弧炉炼钢时,为什么不问功率因数如何,而用过大的电流操作是无益的? [2012-07-30]
三相电弧炉的高压供电线路的电压一般为3300V或10000V,熔化期用变压器最大功率,氧化期用中等功率,还原期用较小功率。
从电弧炉的特性曲线图可知,在一定的电压下,随着电流的增大,电弧炉自电网取得的有效功率增加,到达峰值点以后,继续增大电流,有效功率不但不再增大,反而急剧下降,这是因为整个电弧炉的功率因数显著下降,无功功率增大,因此,不问功率因数如何,而用过大的电流操作是无益的.
- 熔炼铆焊平台铸件时为什么冲天炉炉温越高合金元素的烧损不可能越大? [2012-07-26]
为了满足铆焊平台铁液高温的要求,应尽可能提高冲天炉熔炼温度。炉温不高则不可能获高温铁液。
但是有些中小铸造厂因平时的铁液已是氧化较为严重,生怕炉温提高后,氧化更为严重,合金元素的烧损更大。这种观念是错误的,不敢采用先进技术以获高温,才是应当禁忌的。
冲天炉的炉温绝不是指炉内的平均温度.把氧化区的温度与预热区的温度平均而取一个平均值,对冲天炉熔炼没有意义。通常,冲天炉的炉温指的是过热区中所能达到的最高温度段的温度,即氧化区与还原区交界处的温度。因为其他各处的温度都是由它决定的,只有该段温度高,其他各处的温度才有可能高。当然,由于各厂的冲天炉炉型不同、所用炉料不同、供风制度不同,即使过热区最高温段的温度相同,其他各处的温度亦不尽相同。但是,铁料不管是在哪个炉中熔化,其熔化温度是不变的,因此,熔化带的温度是相同的,刚熔化完的铁液温度是相同的,能达多高的过热度,就要看炉温了。
其实,炉温越高合金的烧损越小早已被生产实践所证实,可是众多人们就是不敢相信或将信将疑,被错误观念束缚而不敢逾越雷池。
- 防止划线平台变形的方法有哪些种? [2012-07-23]
划线平台虽然为厚重型的铸件,但是由于其内在的应力及加工方法等各方面不注意,也会使平台发生形变,影响平台的精度。
1,要注意避免工件和划线平台的工作面有过激的碰撞,防止损坏划线平板的工作面;
2,工件的重量更不可以超过划线平台的额定载荷,否则会造成工作质量降低,还有可能损坏划线平台的结构;
3,为了防止划线平板发生有害的变形,在发装平板时,要将支承支在主支点处。支承时,尽量将平板的工作面调整到水平面内。
4,为了防止平板发生永久变形,检验完毕或划线完毕后,要把工件抬下来,不得长时间放在平板上。
5,使用完毕,要及时擦净平板的工作面,然后涂上一层防锈油。如果比较长时间不用,最好涂上一层黄油,然后铺一层白纸。
6,最好用木板制作的一个专用罩,不用平板时,用罩子将平板罩住。严禁水滴在铸铁平板上。
7,平板要实行周期检定,检定周期要根据使用的具体情况确定,一般为1年。
8,在使用划线平板的过程中要注意不要在潮湿,有腐蚀、过高和过低的温度环境下使用和存放。
只有在各个环节保证好,才能有效的保证其划线平台的平面精度。
- 装配平台的规格及使用注意事项 [2012-07-19]
装配平台主要应用于大型动力机械设备的组装及调试,表面带有T形槽,可以固定动力机械设备,要求较大的装配平台,几块平台可以拼装成大型的平台。
装配平板(装配平台)的规格:平板的规格和实际允许有少许误差装配平板的长、宽、高对角线等,一般都在±0.02(a或b)之间,平板的高度要求:630×630的平板 在220至140之1000×1000至800×800的铸铁装配平板(装配平台)高度在300至400之间;1600×1000以上的装配平板(装配平台)高度在400以上。
装配平板(装配平台)工作面的精度正常使用下可保持2年不变,平板磨损严重后可以通过调试或刮研工艺恢复精度,装配平板(装配平台)本身的使用寿命可以达到50-80年,在使用过程中要注意不要在阴暗潮湿,有腐蚀、过高和过低的温度环境下使用,在使用完装配平台后,要把装配平台的工作面擦净,涂上无水酸性的防锈油,覆盖防潮纸,置于清洁干燥处存放,这样才可以延长装配平板(装配平台)的使用寿命,保证工作质量。
- 检验平台在压砂时怎样增加吸附力 [2012-07-15]
要增加检验平台间附吸力,除了提高平面性以外,控制压砂剂的数量也很重要。压砂剂过多,检验平台间隙也大,附吸力变小,只起研磨作用。究竟压砂时放置多少金刚砂合适?设用w1砂子布满200mm×200mm×10-3=40立方毫米=(3.42mm)3。这个数量显然比实际压入两块检验平台间的砂子数要大得多,即使经过多次压砂,也不可能将检验平台压得这么密集。尤其是多次压砂反而会将原先压入的砂子挤翻出来,同时因热变形,反而压不上砂。所以压砂要求在很短时间内压得好,一般一至二次完成。
其它成份,如硬脂和煤油也很重要。硬脂过多,增加检验平台板间隙,虽然研合力较大,但也压不上;少了润滑性不好。煤油过多,附吸力减小了,而压砂剂太干,则又无附吸力。
检验平台压砂是量块修理工作的重要环节。因为光洁度在▽12以上的加工,只有采取干研方法,干研就是指使用压砂检验平台研磨。检验平台压不上砂,好比机床无切削刀具,加工就无从谈起。有不少用户反映检验平台压不上砂,或不容易压上砂,或压得不牢、压得不多等等。
由于各地压砂方法、使用辅料等不完全相同,所以很难找出一条准确答案。但是,只要符合一定的压砂条件,就能压上、压好。
对200mm×200mm检验平台压W1金刚砂曾作过实测,结果是:检验平台自重11公斤,外加压力约18公斤,附吸力171公斤。因此总的压砂作用力为210公斤。由此可见,压砂的作用主要是两块检验平台附吸的力量,靠检验平台自重和外加力很有限,因此要注意加大附吸力。